In the race to electrify transportation and decarbonise energy systems, lithium-ion batteries have become the cornerstone of the energy transition. But as the world shifts gears, a new challenge has emerged: how do we responsibly and efficiently recycle lithium, one of the most critical ingredients in these batteries?
With batteries representing 90% of global lithium demand, establishing a circular loop for lithium is not optional but existential.
At Viridian Lithium, we believe the answer lies in one overlooked but essential link in the battery value chain: lithium refining.
Refining is what transforms low-grade material into a high-purity product. Viridian Lithium is building the bridge between lithium salts recovered from black mass processing and battery-grade lithium hydroxide.
Europe’s battery boom and the recycling bottleneck
While demand for electric vehicles (EVs) and stationary storage solutions is projected to soar by the end of the decade, the European battery recycling ecosystem faces a sobering reality. In 2024, nearly two-thirds of the projected European black mass processing capacity by 2030 was delayed or cancelled.
The reasons are manifold: slowing EV sales, hesitation around battery chemistries (notably LFP vs. NMC), and regulatory inconsistencies that created uncertainty across the value chain.
Yet, the need to recycle lithium has never been more evident. We estimate that 125,000 tonnes of black mass processing capacities are still in development, meaning that Europe will need to establish refining capacity to purify a minimum of 35,000 tonnes of lithium carbonate equivalent (LCE) recycled lithium annually to battery-grade specifications.
No circular loop for lithium without refining
Unlike other critical minerals, such as nickel or cobalt, lithium cannot be recycled in an open-loop system. Its recovery at end-of-life requires meeting rigorous Battery Grade (BG) standards specifications. Without this, Europe’s recycled lithium may end up as waste or be exported to other regions for further processing. Refiners alone can economically and technically purify recycled lithium salts such as lithium carbonate (LC) or lithium sulphate (LS) to high purity battery grade lithium, be it Battery Grade Lithium Carbonate (BG LC) or Battery Grade Lithium Hydroxide Monohydrate (BG LHM). Through direct refining or blending with virgin lithium compounds, Europe’s lithium refining hubs will unlock a closed loop for lithium, helping meet EU Battery Regulation’s minimum recycled content requirements and contributing to EU lithium supply security.
That is why Viridian Lithium has made it its mission to fill the void in Europe’s circular lithium economy. Our project in Lauterbourg will produce 28,500 tonnes of BG LHM annually, equivalent to 10% of Europe’s needs in 2030—and crucially, we’re building the capacity to integrate recycled feedstock directly into our refining process.
Navigating regulation and opportunity
The European Union’s Battery Regulation (EU 2023/1542) sets ambitious goals:
-
- 6% recycled lithium in batteries from 2031, increasing to 12% by 2036
- 80% lithium recovery efficiency by 2031
Up to March 2025, delegated acts had left room for some inconsistencies, but recent developments support regional set-ups and closed-loop applications:
-
- Black mass now classified as hazardous waste (March 2025)
- Ensuring a level playing field for various battery chemistries (LFP vs NMC, notably)
While progress has been made, gaps remain:
-
- Design calculation, verification and traceability rules that can be enforced on imported materials
- Ensure efficient waste transport within the EU
- Incentivise recycling in Europe
- Clarify methodologies for carbon footprint (LCA) attribution, such as mass allocation vs. economic allocation
To support the growth of a resilient recycling market, the EU must ensure that midstream processors (refiners, pCAM, CAM) like Viridian Lithium are fully integrated into both policy frameworks and industrial ecosystems.
The technical puzzle of recycled lithium
Recycling lithium is not just about chemistry; it is a logistics and quality control conundrum. Black mass processors deal with highly variable and unpredictable feedstock, while cathode manufacturers demand incredibly consistent purity. Variability of a few parts per million in impurities can lead to months of costly requalification. This is where refining adds critical value. At Viridian Lithium, we advocate mass balance and controlled blending, which allow for traceability, consistency and compliance with regulatory recycled content thresholds. By doing so, we help recyclers unlock full value from their material and avoid being trapped in a cycle of failed qualifications.
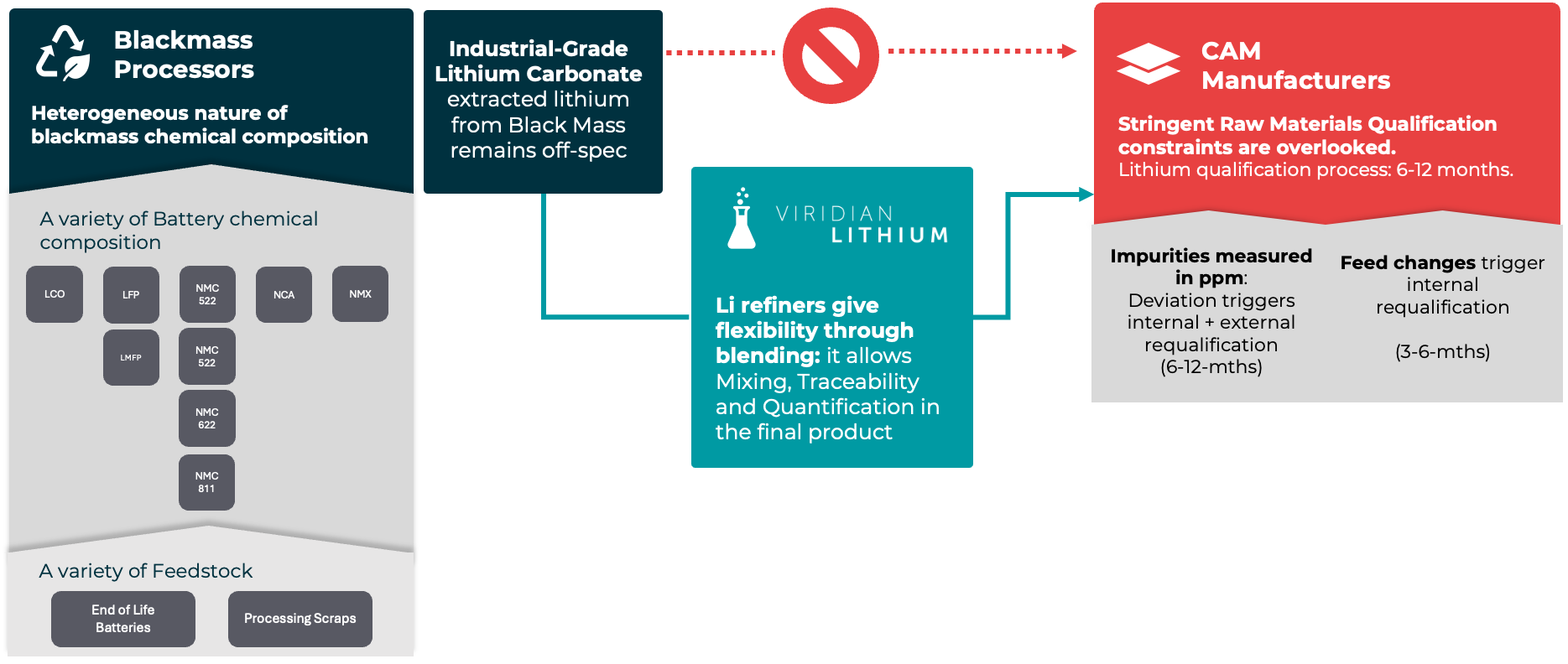
Recycling tech: fragmented and under-optimised
Most recycling projects in Europe are focused on nickel and cobalt, with lithium often treated as a secondary recovery product. As noted in research by Fraunhofer ISI, lithium recovery pathways are still at a low technological maturity.
Today, two main lithium recovery routes are deployed at scale:
- Recovery to Lithium carbonate (Li₂CO₃)
- Recovery to Lithium sulphate (Li₂SO₄)
However, most projects operate at a scale below 2,000 tonnes LCE/year, which lacks the critical size for economic viability for lithium purification to battery-grade standards. That is why Viridian Lithium’s Lauterbourg plant is designed to act as a refining hub for recycled lithium, blending feedstocks and processing diverse compounds from 2028 onward.
Pioneering a low-carbon standard
We are not just aiming for technical excellence; we are setting a new environmental benchmark. Thanks to process optimisation and access to France’s low-carbon electricity mix, Viridian Lithium’s refining process is expected to emit 1.5kg CO₂ per kg of BG LHM—including Scope 1, 2 and 3 emissions according to our in-house pre-FEED Life Cycle Assessment. Depending on the origin of lithium carbonate, this could reduce up to 70% of the BG LHM product’s carbon footprint relative to Chinese-made equivalents.
The use of recycled lithium carbonate could push this even further, depending on life cycle assessment methodologies such as mass or economic allocation.
A roadmap to Europe’s lithium sovereignty
Viridian Lithium is on track to become operational by 2028:
-
- Site preparation: to be completed by June 2025
- Full permitting: to be completed by Q1 2026
- Start of production: 2028
By 2029, beyond phase 1, our Lithium Recovery Unit (LRU) will enable Viridian Lithium to process more diverse and challenging recycled lithium compounds, further strengthening Europe’s independence from foreign suppliers.